Auswahl und Implementierung der richtigen Schutzeinrichtung
- Kommentare: 2
- Sicher arbeiten
- Artikel als PDF herunterladen
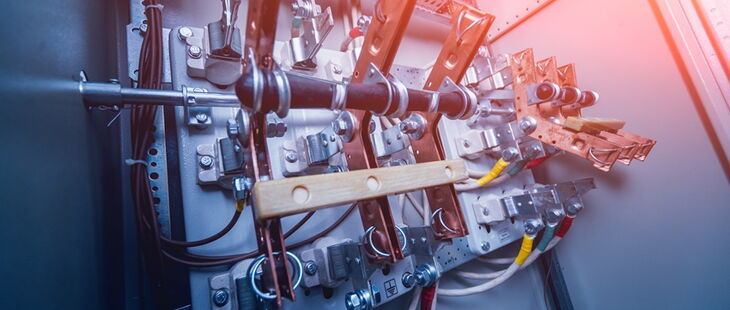
Zur Gewährleistung eines unfallfreien Arbeitens für Ihre Mitarbeiter, ist die Bereitstellung sicherer Maschinen eine wichtige Voraussetzung. Dies erreichen Sie mit der Erstellung eines ganzheitlichen Sicherheitskonzepts.
Im Rahmen eines Sicherheitskonzepts sind alle Betriebszustände der Maschine zu berücksichtigen, Schlupflöcher zu beseitigen, alle Gefährdungen zu identifizieren und die notwendigen Schutzeinrichtungen auszuwählen. Wie Sie bei der Erstellung eines Sicherheitskonzepts vorgehen, konnten Sie bereits in dem Expertenbeitrag „Sichere elektrische Anlagen“ nachlesen.
In dem vorliegenden Beispiel wird nun die praktische Umsetzung ausgeführt und anschaulich erläutert.
Praxisbeispiel zur Auswahl und Implementierung einer Schutzeinrichtung mit Annäherungsreaktion
Ausgangssituation
Um ein optimales Wickelbild zu erzielen, muss das Produkt am Aufwickler einer Anlage zur Längenfertigung (Glasfaserkabel) manuell durch einen Maschinenbediener geführt werden. Durch die relativ hohe Steifigkeit des Produkts muss das Kabel mit hoher Zugkraft aufgewickelt werden, weswegen der Aufwickler mit einem hohen Drehmoment betrieben wird.
Im Zuge einer Gefährdungsbeurteilung wurden erhebliche mechanische Gefährdungsarten an diesem Arbeitsplatz festgestellt, da das Produkt während des Produktionsprozesses vom Maschinenbediener per Hand geführt werden muss, woraus sich die Gefahr des Erfassens, Einziehens bzw. Aufwickelns der Person ergibt. Die bisher einzige für diesen Fall vorgesehene Schutzeinrichtung ist ein Schaltbügel, der oberhalb der Spule (ähnlich einer Not-Reißleine) angebracht ist. Dieser Schaltbügel wird im Falle einer eintretenden Gefahr mit den Füßen der eingezogenen Person betätigt, woraufhin der Aufwickler sofort in Not-Halt geschaltet wird. Nach dem Betätigen des Schaltbügels muss der Positionsschalter manuell entriegelt und der Aufwickler in Bereitschaft zurückgesetzt werden. Durch eine in der Zwischenzeit erhebliche Geschwindigkeitserhöhung der gesamten Anlage und der damit einhergehenden Erhöhung der Drehzahl der Wickelspule ergeben sich eine wesentliche Risikoerhöhung und damit zusätzliche Gefährdungen. Einerseits verringert sich die Reaktionszeit der eingezogenen Person, den Schutzbügel zu betätigen, andererseits hängt die Betätigung des Schaltbügels auch von der Größe der Person ab.
Erste Versuche, eine Schutzweste mit integrierten Kontakten zu verwenden, die der Maschinenbediener während der Produktion trägt, erwiesen sich sehr schnell als unwirksam, da die Schutzweste über ein Spiralkabel mit dem Aufwickler verbunden war. Durch das Spiralkabel entstanden wiederum weitere Gefährdungen durch die Gefahr des Erfassens und Einziehens.
Zielsetzung
Es wurde beschlossen, zusätzlich zu der vorhandenen durch Berührung wirkenden Schutzeinrichtung (Schaltbügel) einen Bereich mit Aufenthaltsüberwachung in das Sicherheitskonzept zu integrieren. Dabei musste zunächst der Aufenthaltsbereich des Maschinenbedieners definiert werden, den es dann mithilfe von Schutzeinrichtungen mit Annäherungsreaktion zu überwachen gilt. Dabei soll die Präsenz des Maschinenbedieners sichergestellt werden, d.h., wird die Person durch das Kabel bzw. die Spule mitgezogen, verschwindet sie aus dem überwachten Bereich, die Maschine erkennt diesen Zustand als Fehler und schaltet den Aufwickler sofort in Not-Halt.
Auswahl einer Schutzeinrichtung
In einem ersten Schritt musste entschieden werden, ob druckempfindliche (Sicherheits-Trittmatten) oder berührungslos wirkende Schutzeinrichtungen eingesetzt werden. Von einem Einsatz der Sicherheits-Trittmatten wurde jedoch schnell abgesehen, da diese ein hohes Potenzial zum Umgehen der Sicherheitseinrichtung aufweisen (z.B. Abstellen von Gegenständen, Stuhl usw.). Die Wahl fiel stattdessen auf einen Sicherheits-Laserscanner, mit dem verschiedene
Erkennungsbereiche/Erkennungsfelder konfiguriert werden können. Dies ist wichtig, da an dem Aufwickler, je nach Produkt, unterschiedlich breite Spulen eingesetzt werden.
Funktionsprinzip
Der Aufenthaltsbereich soll über zwei Überwachungsfelder definiert werden, die vorher drahtbruchsicher in die SPS des Aufwicklers programmiert werden.
Durch Betreten des Erkennungsbereichs 1 (rot) wird die Überwachung aktiviert. Ein Betreten durch die Schleuse (Erkennungsbereich 2, grün) ist nicht zwingend erforderlich, der überwachte Bereich kann auch von der Seite betreten werden. Die Meldelampe „Überwachung ein“ H21 ist an.
Zum Verlassen des überwachten Bereichs muss durch die Schleuse gegangen werden. Wird Erkennungsbereich 1 nicht durch die Schleuse verlassen, erfolgt eine Zwangsabschaltung.
Meldelampe „Überwachung ein“ H21 geht wieder aus. Meldelampe „Überwachung ausgelöst“ H22 ist an.
Befinden sich zwei Personen im Erkennungsbereich 1, muss die Anlage im Fehlerfall durch den Not-Aus-Taster abgeschaltet werden. Befinden sich zwei Personen im Erkennungsbereich 1 und verlässt eine diesen durch die Schleuse, wird die im Erkennungsbereich 1 verbleibende Person überwacht. Darin liegt der große Vorteil dieser Anwendung.

Umsetzung
Um sicherzustellen, dass der Maschinenbediener Erkennungsbereich 1 (rot) nicht seitlich, sondern durch die Schleuse (Erkennungsbereich 2 – grün) verlässt, wurden seitlich zusätzliche Schutzgitter angebracht.
Mithilfe der Laserscanner-Software wurden vier unterschiedliche Erkennungsbereiche in Abhängigkeit von den Spulenbreiten parametriert, die vorher im Bedienpanel des Aufwicklers angewählt werden können. Diese werden dann durch Ausgänge der SPS des Aufwicklers mit den Steuereingängen des Laserscanners verknüpft.

Abhängig von der Eingabe der Spulenbreite wird ein Erkennungsbereich definiert. Zur Auswahl stehen vier Erkennungsbereiche, die grau hinterlegt sind. Der aktive Erkennungsbereich wird farbig dargestellt.
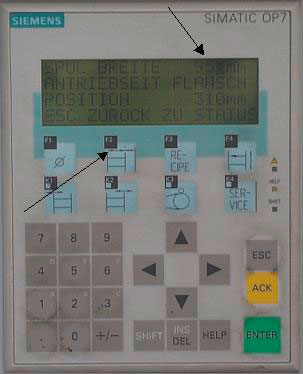
Wichtig
Eine falsche Eingabe bietet keinen Personenschutz! Die Personenschutzüberwachung findet nur im Automatikmodus statt.
Mögliche Fehlerquellen:
- Der Operator gibt eine falsche Spulenbreite ein: Der Abwickler verletzt permanent den Erkennungsbereich 1 keine Abschaltung.
- Der Operator stellt einen Gegenstand im Erkennungsbereich 1 ab: Der Gegenstand verletzt permanent den Erkennungsbereich 1 keine Abschaltung.
- Der Operator stellt einen Stuhl in die Schleuse: Der Stuhl verletzt permanent den Erkennungsbereich 2.
- Die Überwachung ist abgeschaltet. Eine Abschaltung erfolgt durch verschmutzte Fenster: Fenster reinigen mit weichem Tuch und Glasreiniger. Achtung: MEK zerstört die Kunststofffenster.
- Abschaltung erfolgt durch lose Holzteile, welche beim Rotieren durch das Fenster fallen: Spulen mit besserer Qualität verwenden
- Die Abschaltung erfolgt, weil der Operator seitlich aus dem überwachten Bereich getreten ist. beim Verlassen durch die Schleuse gehen
Nachtrag
Nach zwei Jahren in Betrieb wurden sporadische Fehlfunktionen im System des Laserscanners festgestellt. Meist in den Sommermonaten kam es oftmals ohne erkennbaren Grund zu Fehlabschaltungen des Aufwicklers. Als Ursache wurde einfallendes Sonnenlicht auf die Empfängereinheit des Laserscanners festgestellt.
Des Weiteren kam es auch öfter zu Abschaltungen durch herabfallende Späne und Schmutz von den Holzspulen. Um eine höhere Maschinensicherheit und weniger Produktionsausfälle zu erreichen, wurde die Sicherheitseinrichtung durch die Maschinenbediener sehr oft durch Abkleben umgangen.
Ein weiteres Problem stellten zusätzlich eingeführte Holzspulen dar, deren Maße nicht den „Standard“-Spulen entsprachen und somit keine zusätzlichen Erkennungsbereiche dem Laserscanner hinzugefügt werden konnten. Während des Betriebs passierte es deswegen oftmals, dass der Maschinenbediener versehentlich den Erkennungsbereich 1 verließ und es damit zu Abschaltungen des Systems kam.
Um den gewünschten Sicherheitsstandard wiederherzustellen, wurde entschieden, eine andere berührungslose Sicherheitseinrichtung in den Aufwicklern zu installieren.
Mithilfe von Sicherheits-Lichtvorhängen, die nur auf eine bestimmte Wellenlänge getrimmt sind und somit nicht von Sonneneinstrahlung beeinflusst werden, kann das bisherige Funktionsprinzip beibehalten werden. Ein weiterer positiver Effekt ist, dass keine Erkennungsbereiche definiert werden müssen, durch die seitliche Anordnung keine Totzonen entstehen und das Sicherheitssystem nicht von der Spulenbreite abhängig ist.
Um Manipulationen durch „Übersteigen“ der Sicherheitseinrichtung zu vermeiden, wurden am Aufwickler seitlich zusätzliche Schutzgitter angebracht, sodass der Maschinenbediener durch Passieren des Erkennungsbereichs 2 den Gefahrenbereich verlassen muss und das System damit wieder abschaltet.
Der Sicherheits-Lichtvorhang für Erkennungsbereich 2 wurde schräg angeordnet, damit er nicht „überstiegen“ werden kann und gleichzeitig schneller durchschritten wird.
Die ausgetauschte berührungslose Sicherheitseinrichtung hat sich bisher als sehr wartungsarm, zuverlässig, robust und ausfallsicher herausgestellt.
Kommentare
Kommentar von Alfons |
Ich frage mich, wer die Verantwortung trägt, denn für mich ist das eine wesentliche Veränderung der Maschine. Und das hat doch was mit CE Kennzeichnung zu tun, nicht aber mit Elektrosicherheit.
Kommentar von Dirk |
Warum wird das Aufwickeln überhaupt manuell durch einen Bediener erledigt?? Eine automatisierte Lösung wäre mindestens genau so effektiv und man könnte den Bereich auch sehr sicher gestalten.
Einen Kommentar schreiben